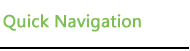

![]() |
Biological base plastic
Film Blowing Grade Starch Based Biodegradable Master Batch
Product Features:
Granules are in light yellow and come in cylinder and round shape, with slight fragrance. They absorb moisture easily and are easily decomposed by microbes. They are anti-static. The processing temperature of them is lower than that of conventional plastic. They are easily colored. Such resin is a kind of additive which should be blended with polyolefin materials like PE, PP, PVA, EVA, etc. to process finish products. It can be 100% degraded within 2 to 2.5 years in the laboratory conditions.
Product Testing:
● The degradation rate in 100 days is up to the adding ratio of it.
● Biodegradation can be achieved when blended with conventional plastic, like PE, PP, PVA, EVA, etc.
Properties and Data:
Testing Item | Standard | Unit | Result |
Appearance | | | Light Yellow |
Density | GB 1033 | g/ cm3 | 1.10 – 1.25 |
Moisture Content | | % | 0.6– 1.5 |
Melt Flow Index | GB3682 | g/10 min | 0 - 2 |
Tear strength | GB 1040 | MPa | ≥15 |
Elongation | GB 1040 | % | ≥300 |
Bio Substances Content | | % | ≥90 |
n-hexane Extracts | GB/T5009.58 | % | ≤4.0 |
Rockwell hardness | GB9342 | R gauge | |
Softening point | GB/1633 | ºC | >65 |
Degradation rate in 100days | Degradation rate is affected by the adding ratio. | ||
The data for tensile strength and elongation refer to that of finished film products. |
Recommended Applications:
For all sorts of anti-static packing purposes, e.g. electronic product packaging, car interior covering film, electrical appliance packaging, agricultural mulch film, shopping bags, T-shirt bags, document folders, filter bags, storage bags, bin bags, tear-on-roll bags, disposable gloves, table cloths, aprons and rain coats, etc.
Processing Equipment:
Common film blowing extruder, sheet extruder, bag making machine, printers, and heat sealing machines are all can be used.
Processing Technology:
● Best results will be achieved with a screw L/D ratio ≥ 28:1. The blow-up ratio should be more than 1:3 to obtain the maximum production yield and the best quality.
● LT-M
● Newly made f, ilm feels brittle, or crispy. Its elongation is low. This is due to severe dehydration during production. Therefore, the film needs to be settled for a 24- hour curing period to regain elongation and anti-tear strength before being used to make finish products, e.g. bag-making or printing.
● The minimum thickness of film made of such material can be 10 microns.
Remarks:
● The price of LT-M
● Due to the high starch content, the resin easily absorbs moisture. So it needs to be stored in a dry environment. The package should also be sealed properly to prevent the ingress of moisture.
● In case the resin is damp, it should be dried for 2 hours at 80ºC.
● Its processing temperature is 5ºC to 10ºC lower than that of PE. During processing, the temperature is correct when corn starch fragrance can be smelled at the hopper.
● It can be easily decomposed into soil friendly substances in microbial environment.